Rail Mounted Gantry (RMG) container cranes are critical for efficient cargo handling in ports and intermodal yards. However, their installation can present several challenges that require careful planning, skilled execution, and a deep understanding of site-specific factors. Addressing these challenges effectively ensures the crane operates optimally and delivers long-term value. This article explores the common obstacles encountered during RMG crane installation and offers strategies to overcome them.
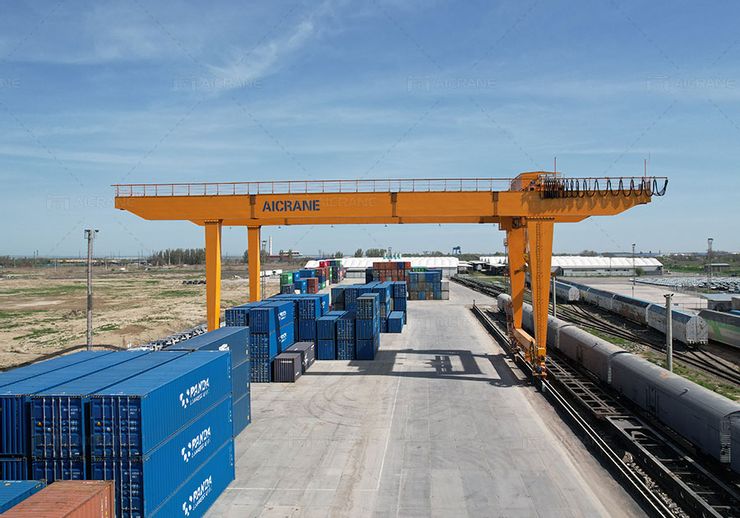
RMG Container Crane
1. Site Preparation Challenges
The foundation of an RMG container crane operation lies in proper site preparation. This involves ensuring that the installation site is level, structurally sound, and meets all technical requirements.Challenges:
- Uneven Terrain: Many installation sites require significant leveling and grading before construction can begin.
- Soil Stability: Weak or unstable soil may necessitate additional groundwork, such as piling or soil reinforcement.
- Environmental Restrictions: Ports and rail yards often have strict environmental regulations, which can limit certain construction activities.
Solutions:
- Conduct thorough geotechnical surveys to assess soil conditions.
- Use advanced leveling techniques, such as laser-guided grading, for precision.
- Collaborate with environmental consultants to navigate regulatory requirements.
2. Transportation and Logistics
RMG cranes are massive structures, and transporting their components to the installation site can be a logistical challenge.
Challenges:
- Oversized Components: The large size of crane parts often requires special transportation permits and equipment.
- Distance to Site: Remote locations or sites with limited access can complicate delivery.
- Weather Conditions: Adverse weather, such as strong winds or heavy rains, can delay transportation and unloading.
Solutions:
- Plan transportation routes carefully, considering restrictions on oversized loads.
- Schedule deliveries during favorable weather and low-traffic periods.
- Utilize modular crane designs that allow components to be transported and assembled in smaller sections.
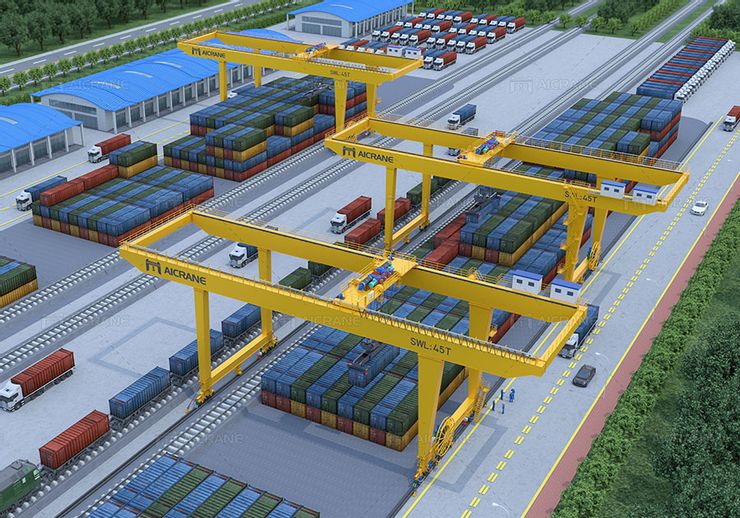
Rail Mounted Container Gantry Cranes
3. Assembly and Alignment Issues
The assembly of a rail mounted gantry crane involves precise alignment and installation of its structural components, mechanical systems, and electrical wiring.
Challenges:
- Complex Assembly: The intricate design of RMG cranes requires skilled labor and specialized equipment.
- Alignment Errors: Misalignment during assembly can lead to operational inefficiencies and increased wear and tear.
- Integration of Systems: Ensuring that mechanical and electrical systems work seamlessly together can be challenging.
Solutions:
- Employ experienced installation teams with expertise in RMG crane assembly.
- Use laser-guided or GPS-based alignment tools for precision.
- Test mechanical and electrical systems thoroughly before commissioning.
4. Safety Concerns
Safety is paramount during the installation of heavy machinery like RMG cranes. Accidents can result in injuries, delays, and additional costs.
Challenges:
- Heavy Lifting: Lifting and positioning massive crane components pose significant risks.
- Worker Safety: High-altitude work and the use of heavy equipment increase the potential for accidents.
- Equipment Failure: Malfunctioning equipment can lead to accidents or delays.
Solutions:
- Implement rigorous safety protocols, including the use of personal protective equipment (PPE).
- Train workers in safe lifting techniques and emergency response procedures.
- Conduct regular inspections of all installation equipment.
5. Electrical and Control System Installation
RMG cranes rely on advanced electrical and control systems for their operation. Installing these systems can be complex and time-consuming.
Challenges:
- Complex Wiring: The extensive wiring required for power, controls, and communication systems can be difficult to manage.
- System Integration: Ensuring compatibility between various subsystems, such as anti-sway controls and remote operation systems, can be challenging.
- Testing and Calibration: Proper testing and calibration are essential to ensure the crane functions as intended.
Solutions:
- Use detailed schematics and labels to streamline the wiring process.
- Collaborate with experienced electrical engineers to ensure seamless system integration.
- Allocate sufficient time for thorough testing and calibration.
6. Regulatory Compliance
Installation projects must comply with local, national, and international regulations, which can vary widely.
Challenges:
- Permitting Delays: Obtaining necessary permits can be a lengthy process.
- Standards Compliance: Meeting industry standards, such as ISO or OSHA requirements, adds complexity to the installation process.
- Environmental Impact Assessments: Conducting and addressing the results of these assessments can delay projects.
Solutions:
- Work with regulatory experts to expedite the permitting process.
- Use certified components and adhere to industry best practices to ensure compliance.
- Address environmental concerns proactively to avoid project interruptions.
7. Budget and Timeline Management
Large-scale projects like RMG crane installations often face budget overruns and timeline delays.
Challenges:
- Unexpected Costs: Issues such as soil instability or equipment failure can increase costs.
- Delays: Weather, logistics, or technical problems can push back project timelines.
- Resource Allocation: Ensuring adequate manpower and materials at each stage of installation is critical.
Solutions:
- Build contingency funds into the project budget to cover unforeseen expenses.
- Develop a detailed project timeline with milestones and regular progress reviews.
- Use project management software to coordinate resources effectively.
Conclusion
Installing an RMG container crane is a complex process that requires meticulous planning, skilled execution, and a proactive approach to overcoming challenges. From site preparation and transportation to assembly, safety, and compliance, each phase presents unique obstacles. By addressing these challenges with innovative solutions and best practices, businesses can ensure a smooth installation process and maximize the operational benefits of their RMG cranes. Investing in professional installation services and robust project management tools can make all the difference in achieving success.