Double girder overhead cranes are indispensable in various industries, such as manufacturing, construction, and warehousing, where heavy loads need to be lifted and transported efficiently. However, like any other machinery, these cranes are prone to unexpected downtime due to mechanical failures, electrical issues, or operator errors. Handling such downtime effectively is crucial to minimize productivity losses and ensure safety in the workplace.
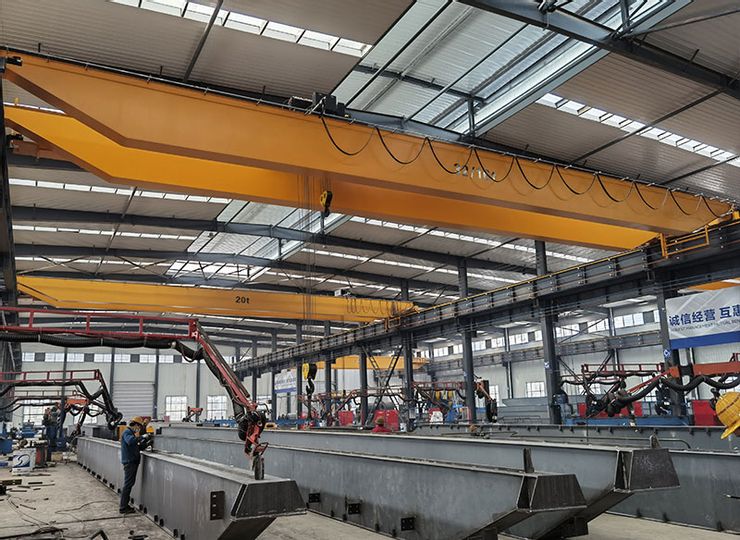
1. Understanding the Causes of Downtime
Before addressing unexpected downtime, it’s essential to identify its root causes. Common issues include:- Mechanical Failures: Worn-out hoist mechanisms, broken wires, or misaligned components can lead to operational halts.
- Electrical Issues: Faulty wiring, power surges, or damaged circuit boards may disrupt the crane’s functionality.
- Overloading: Lifting loads beyond the double girder overhead crane capacity can damage its structure and components.
- Operator Errors: Improper handling or lack of training can result in accidents or equipment damage.
- Environmental Factors: Extreme weather, humidity, or dust can affect the crane’s performance.
Understanding these causes helps in formulating an effective action plan to address downtime and prevent recurrence.
2. Immediate Steps to Take During Downtime
When downtime occurs, follow these steps to ensure safety and restore operations promptly:
a) Ensure Safety First
- Shut down the crane and disconnect it from the power source.
- Evacuate the immediate area to prevent accidents.
- Inform all personnel about the downtime and restrict access to the affected zone.
b) Assess the Situation
- Inspect the crane for visible damage or malfunctions.
- Identify if the issue is mechanical, electrical, or operational.
- Check for error codes or alarms on the crane’s control panel.
c) Notify the Maintenance Team
- Contact the on-site maintenance team or a qualified service provider.
- Provide detailed information about the issue to facilitate quick diagnosis.
d) Document the Incident
- Record the downtime details, including the date, time, suspected cause, and actions taken. This information can help in future troubleshooting and preventive measures.
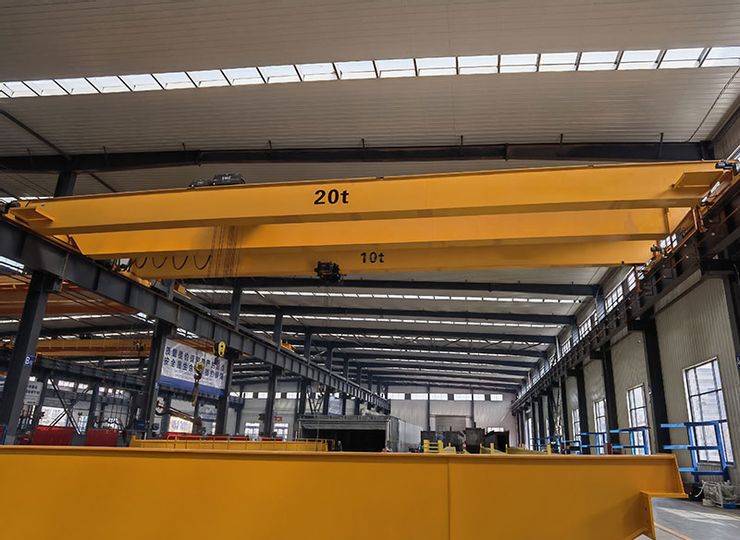
3. Repair and Recovery Process
Efficient repair and recovery are key to minimizing downtime. Here’s how to approach this:
a) Diagnose the Problem
- Use diagnostic tools and equipment to identify the root cause of the issue.
- Consult the crane’s manual or contact the manufacturer for guidance.
b) Perform Repairs
- Replace damaged components with high-quality, compatible parts.
- Address electrical issues by inspecting and repairing wiring, circuit boards, and fuses.
- Lubricate and align mechanical components as needed.
c) Test the Crane
- Conduct a trial run to ensure the crane operates smoothly and safely.
- Verify that all safety features, such as limit switches and emergency stop mechanisms, are functional.
d) Resume Operations
- Inform the team about the crane’s readiness and implement any necessary safety protocols.
4. Preventing Future Downtime
Preventive measures can significantly reduce the likelihood of unexpected downtime. Implement the following practices:
a) Regular Maintenance
- Adhere to a scheduled maintenance plan that includes inspecting, cleaning, and servicing the double girder eot crane.
- Replace worn-out parts proactively to prevent sudden failures.
b) Operator Training
- Ensure that operators are adequately trained to handle the crane safely and efficiently.
- Conduct refresher courses to keep operators updated on best practices.
c) Monitoring and Diagnostics
- Use advanced monitoring systems to track the crane’s performance and detect potential issues early.
- Analyze data to predict and prevent failures.
d) Environmental Protection
- Install protective measures, such as covers or enclosures, to shield the crane from adverse environmental conditions.
- Use corrosion-resistant materials in high-humidity areas.
e) Load Management
- Avoid exceeding the crane’s rated capacity.
- Use proper rigging techniques to ensure balanced and secure lifting.
5. Developing a Downtime Response Plan
Having a well-defined response plan can expedite recovery and minimize disruptions. A comprehensive plan should include:
- Emergency Contact List: Maintain a list of key personnel, including operators, maintenance staff, and service providers.
- Spare Parts Inventory: Keep an inventory of critical spare parts to facilitate quick repairs.
- Training Programs: Conduct regular drills to prepare staff for handling downtime scenarios.
- Communication Protocols: Establish clear communication channels to keep all stakeholders informed.
6. Leveraging Technology
Modern technology can enhance the reliability and efficiency of double girder overhead cranes. Consider the following innovations:
- IoT Sensors: Install sensors to monitor the crane’s condition and provide real-time alerts.
- Predictive Maintenance Tools: Use AI-driven tools to predict potential failures and schedule maintenance accordingly.
- Remote Monitoring Systems: Enable remote access to the crane’s diagnostics and controls for quicker troubleshooting.
7. Evaluating the Impact of Downtime
Post-recovery, evaluate the impact of the downtime to improve future preparedness. Key aspects to assess include:
- Cost of Repairs: Calculate the expenses incurred for repairs and replacements.
- Productivity Loss: Measure the operational delays and their impact on project timelines.
- Root Cause Analysis: Identify underlying factors and implement corrective actions.
Conclusion
Handling unexpected downtime during double girder overhead crane operations requires a combination of immediate action, efficient repair processes, and preventive measures. By understanding the causes of downtime, implementing regular maintenance, and leveraging modern technology, businesses can minimize disruptions and ensure seamless operations. Developing a robust downtime response plan further enhances readiness, enabling teams to tackle challenges effectively and maintain productivity in the long run. Proactive management and continuous improvement are the keys to maximizing the performance and reliability of double girder overhead cranes.