Gantry cranes play a critical role in various industries, from construction to manufacturing and logistics. Their ability to lift and move heavy loads efficiently makes them indispensable. However, one factor that often influences a buyer's decision is the price of these cranes. The price of a gantry crane can vary significantly depending on multiple factors, one of the most important being the manufacturing technology used. This article explores how advancements and innovations in manufacturing technology directly impact the pricing of gantry cranes.
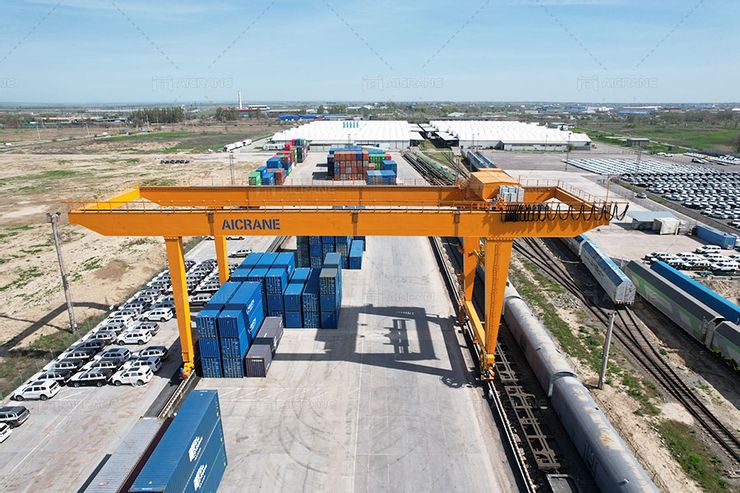
1. Automation in Manufacturing Processes
Automation has transformed the way gantry cranes are manufactured. Automated systems like robotic welding, CNC machining, and advanced assembly lines improve the precision and efficiency of production processes.- Precision and Quality: Automated welding and machining ensure that each component of the gantry crane meets exact specifications. This level of precision reduces defects and rework, leading to higher quality products.
- Reduced Labor Costs: Automation minimizes the need for manual labor in repetitive tasks, which can reduce production costs. However, the initial investment in automation technology may slightly increase the price of gantry crane produced using such methods.
While automation can drive up the initial production cost, the long-term benefits of durability and reliability often justify the price for customers.
2. Use of Advanced Materials
Modern manufacturing technologies enable the use of advanced materials in gantry crane production. For instance, high-strength steel and lightweight alloys are increasingly used to enhance performance.
- Material Costs: High-quality materials often come at a premium, which can increase the overall price of the crane. However, these materials also reduce the weight of the crane without compromising strength, leading to better energy efficiency and lower operating costs.
- Innovations in Material Processing: Techniques such as laser cutting and 3D printing allow for the creation of complex designs and components, further optimizing material usage. Although these technologies can add to production costs, they improve the crane's functionality and lifespan.
3. Smart Technologies and IoT Integration
The integration of smart technologies and the Internet of Things (IoT) in gantry cranes has become a significant trend. Features like remote monitoring, predictive maintenance, and automated controls are becoming standard in modern cranes.
- Cost of Smart Features: Adding sensors, connectivity modules, and software for data analysis can increase the manufacturing cost. However, these features provide significant value by reducing downtime and enhancing safety.
- Value Addition for Customers: Customers are willing to pay a premium for cranes equipped with smart technologies because of the long-term savings and operational efficiency they provide.
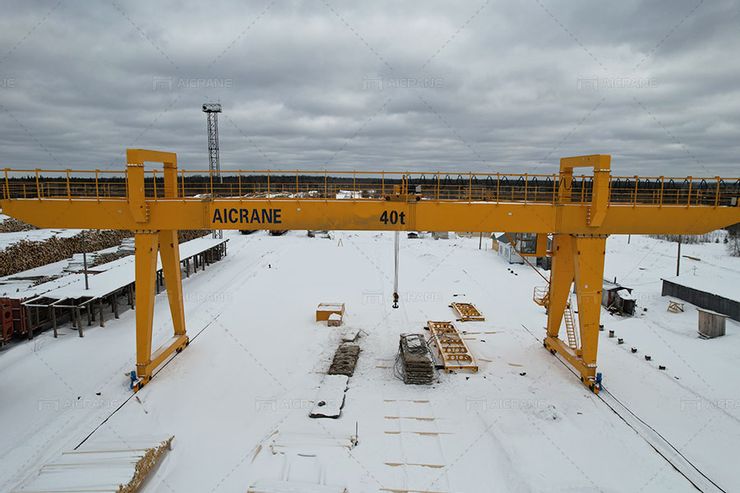
4. Energy-Efficient Design and Manufacturing
Energy efficiency is a priority in the manufacturing of gantry cranes. Modern production techniques focus on reducing energy consumption during both the manufacturing process and the crane's operation.
- Eco-Friendly Manufacturing: Techniques like energy-efficient welding, heat treatment, and painting processes lower the carbon footprint of production but may require higher initial investments in equipment.
- Energy-Saving Components: Features like variable frequency drives (VFDs) and regenerative braking systems improve operational efficiency. While these components can increase the upfront price, they lower energy costs over the crane's lifecycle.
5. Modular Design and Standardization
Manufacturing technology has also enabled modular designs and standardized components in gantry cranes. Modularization simplifies production and assembly, reducing manufacturing time and costs.
- Interchangeable Parts: Standardized components allow manufacturers to produce parts in bulk, lowering costs. Customers benefit from easier maintenance and reduced downtime due to readily available spare parts.
- Customization Costs: While modular designs reduce costs for standard models, highly customized cranes may still command a higher price due to the additional design and production efforts required.
6. Reduced Lead Times
Advanced manufacturing technologies have significantly reduced lead times in gantry crane production. Faster production processes mean gantry crane manufacturers can deliver cranes more quickly to customers.
- Impact on Pricing: While faster production can reduce labor and operational costs, it may not always translate to lower prices. Instead, it adds value for customers by reducing project delays and improving delivery schedules.
- Competitive Advantage: Manufacturers with shorter lead times often attract more customers, even if their prices are slightly higher, due to the added convenience and reliability.
7. Customization Capabilities
Modern manufacturing technology allows for greater flexibility in customizing gantry cranes to meet specific customer needs. From tailored lifting capacities to specialized features, customization is now easier and more precise.
- Cost Implications: Customization often increases production costs due to the need for unique components and additional design work. However, customers are typically willing to pay a premium for a crane that perfectly suits their requirements.
- Customer Satisfaction: Advanced manufacturing processes ensure that customized cranes meet exact specifications, enhancing customer satisfaction and justifying higher prices.
8. Supply Chain Optimization
Technological advancements have also improved supply chain management in gantry crane manufacturing. Efficient logistics and inventory management systems reduce production delays and material waste.
- Cost Savings: Optimized supply chains lower material costs and reduce inventory holding expenses. These savings can either be passed on to customers or used to enhance the product's features.
- Global Sourcing: Technology allows manufacturers to source materials and components globally, balancing quality and cost. However, fluctuations in global supply chains can impact pricing.
9. Impact of Research and Development (R&D)
Investment in R&D drives innovation in gantry crane manufacturing. While R&D expenses can increase production costs, they lead to the development of more advanced and efficient cranes.
- Innovation Costs: Cutting-edge technologies developed through R&D, such as anti-sway systems and advanced control algorithms, can add to the price of a crane.
- Long-Term Benefits: These innovations improve crane performance, safety, and longevity, offering better value for customers.
Conclusion
The impact of manufacturing technology on gantry crane prices is multifaceted. While advanced technologies can increase production costs, they also enhance the crane's quality, efficiency, and features, providing significant value to customers. Buyers must consider these factors when evaluating the price of a gantry crane. Investing in a technologically advanced crane may have a higher upfront cost, but it often leads to long-term savings through improved performance, reduced maintenance, and energy efficiency.
As manufacturing technology continues to evolve, the gantry crane industry is poised to offer even more innovative and cost-effective solutions. For businesses looking to invest in gantry cranes, understanding the role of technology in pricing can help them make informed decisions and achieve the best return on investment.